Acerca de
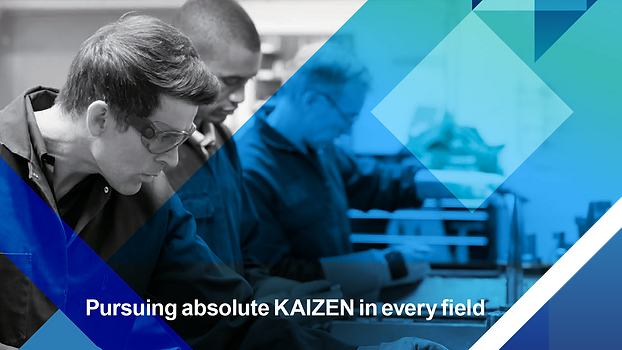

OTRS is video-based time study software designed to help you achieve labor and cost reductions within your operations. The latest version of this work measurement software, OTRS10, leverages Japanese industrial engineering and lean manufacturing principles to help your company achieve world-class performance.
OTRS is considered the gold standard in time and motion study software and is trusted by the biggest names in Japanese industry. The software is currently used by over 6000 customers globally including 87% of Japan's vehicle makers. Now available in English, Japanese and Chinese as standard, and easily configurable to any language through the preparation of a language file, OTRS is rapidly being adopted by a growing user base globally. The latest version, OTRS10, has been developed in collaboration with Toyota Motor Corporation to support the Toyota Production System.
Improve Your Business in 5 Steps

KAIZEN Cycle
-
Shoot video, Analyze the process
-
Eliminate waste, Standardize operation
-
Create video manuals
-
Output reports
-
Skill transfer and staff training
OTRS10 - Software Features

Motion Analysis

Rear range
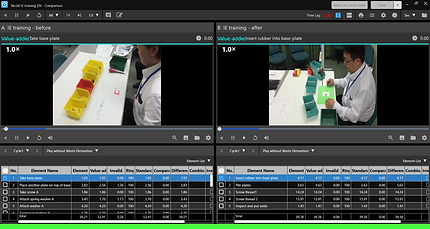
Comparison

Standard Work Combination Chart

Line Balancing Chart

Aggregation
OTRS implementation flow and Implemented cases

Want to reduce the labor, time, and costs associates with work analysis
Typically, work observation is conducted using a stopwatch, but this method makes it difficult to get accurate measurements, resulting in the need to repeat the process many times. With OTRS, an intuitive user interface and “fast-forward” and “frame advance” video control functions enable rapid on-site motion analysis.

Want to create the optimum production process matching our new production efforts
Identified multiple work flows and bottlenecks using the OTRS side-by-side video and work process composition simulation functions. Then performed work recombination/work rearrangement simulations to create new processes and applied them to actual production lines, enabling drastic improvements to daily production output.

Want to rearrange working environment for better technological training and skills transfer
Pre-line production training for new workers used to be "OJT"But with OTRS, new workers shot video and analyzed by themselves, comparing work flow/motions of new workers against experienced workers, which resulted in reducing a great amount of training time.

Want to save manpower by optimizing production process
Conducted simulation to reduce non-value adding tasks using OTRS.Training prior to the actual production line made us significantly reduce on non-value added activities such as walking and idle time.
Our clients




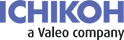














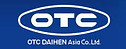



















